Bought on a kickstarter last year, and just arrived. It’s a bit niche, but if you know, you know 😀
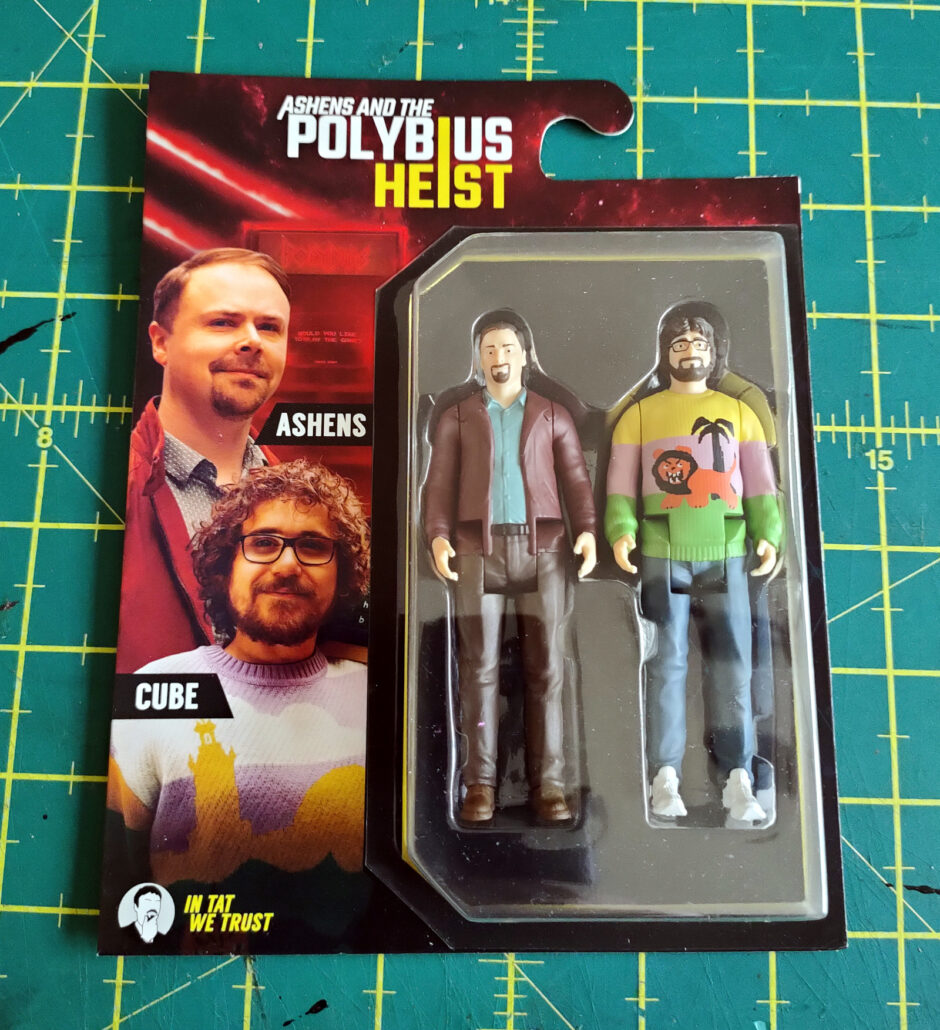
Bought on a kickstarter last year, and just arrived. It’s a bit niche, but if you know, you know 😀
The sister’s birthday was today so made a bag.
It’s a slightly modified version of a @hahn_atelier design:
I made the D-ring attachments slightly different, used a different connection between gusset and front/back panels and added a shoulder pad to the strap. But also, lined it, with french edging around the edges and the internal seams lined as well.
The french edging was made a lot easier with the welt knife.
Made a prototype initially using flooring vinyl.
But the real thing was made using Oceano coloured Maremma leatherv from Tuscany (from Conceria Puccini I believe) sourced from Tatra Leather and using Vinymo thread. Been trying that thread for the last little while and I’m liking it. Got some from Etsy and ordered a kilometre or so of it after working with it for a bit. The 100m spools from Etsy and the like are nice because you can pick out a colour for just one project instead of having to get a kilometre or more of the stuff.
It takes hot foil stamping (120C for 5 seconds) well and it also heat embosses quite well with the stamp at 120C and applying pressure for ten seconds or so.
The shoulder strap has some padding and also acts as an additional keep for the buckle on the strap.
All in all, it came out pretty well. I’m starting to see some actual improvement for once which is nice. Give me a few years and I might actually get good at this!
Just keeping busy now.
And got a new tool. Well. I say new, it was made in the 1950s in Germany, but never bought. New old stock is the term I think.
It’s a welt knife. For cutting welts, obviously. What’s a welt?
The problem is trimming the welt without cutting into the upper leather. The solution was the welt knife – it’s got a blunt runner of sorts on one side of the blade, you run that along the upper and the blade cuts the welt and only the welt. Why do I want it? Because you need to do that for a french edge, where the lining of a piece is glued face-to-face to the outside, stitched, then folded over the top of the piece to the inside, glued again, and stitched again.
Leaves you with a bit to trim off below the second stitch line. Do it with a normal straight knife, you risk cutting into the piece itself. If you flip over the straight knife and cut with the back of the knife running along the piece, you get something of a ragged cut like you see there. The welt knife on the other hand has a blunt runner thing beside the cutting edge:
That lets you do this:
Not a perfect result but not bad for having used it only three or four times. Plus, it cost half the price of a french edger, which is the only other tool I’ve seen used for this. So I’m grand with that.